Let’s face it—your roof is the silent protector of your entire industrial facility. From shielding valuable equipment to keeping operations running smoothly, it’s a key part of your infrastructure. When issues arise, patchwork fixes or hasty decisions can be risky (and expensive). That’s why who you hire to handle industrial roof repairs matters—a lot.
Imagine trusting your car to someone who’s never fixed an engine. It’s the same with roofing. Experience isn’t just a line on a resume—it’s the backbone of successful, safe, and efficient repairs. The more seasoned the contractor, the better the outcome for your facility.
What Makes Industrial Roofing So Complex?
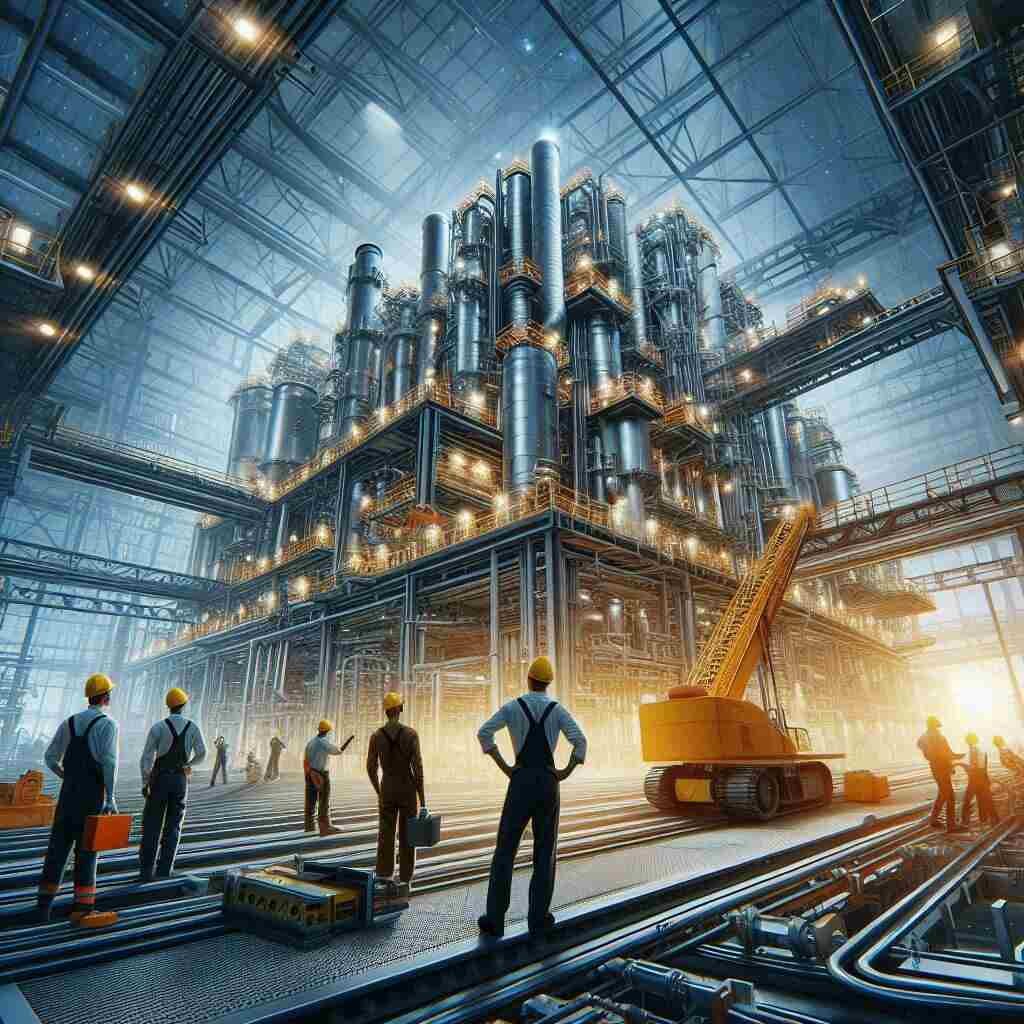
Size and Scope of Industrial Roofs
Industrial roofs aren’t like the ones on your house. They’re massive, often covering tens of thousands of square feet. That alone makes repairs more complicated, requiring large crews, equipment, and careful planning.
Material Differences from Residential Roofs
You’re dealing with materials like TPO, EPDM, metal panels, or modified bitumen—stuff not typically found on a suburban home. Experienced contractors know these materials like the back of their hand.
Safety Regulations and Legal Requirements
Industrial roof work involves strict OSHA regulations, fall protection requirements, and sometimes union labor standards. Mess up here, and it’s not just costly—it can be illegal.
Risks of Hiring Inexperienced Contractors
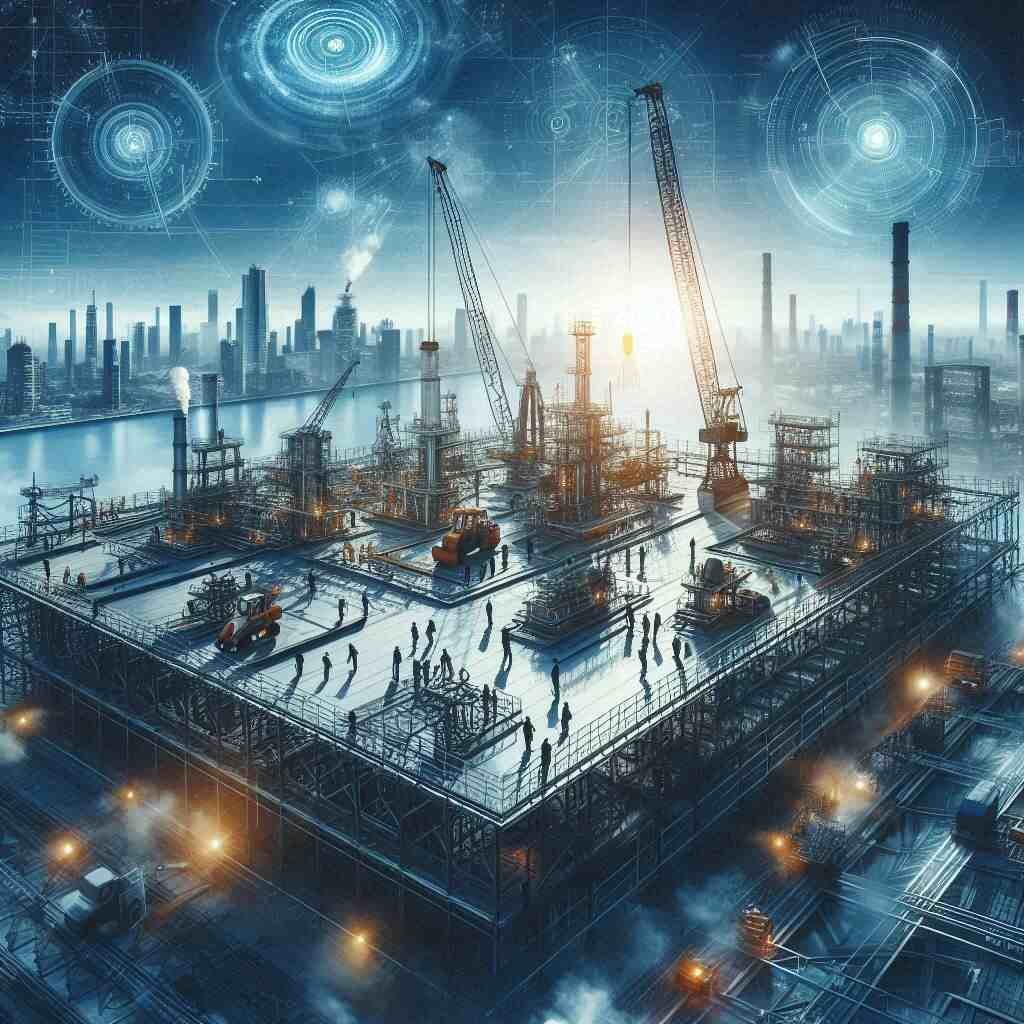
Subpar Workmanship
Inexperienced roofers might not spot structural damage or improperly install membranes, leading to leaks, mold, and even roof collapse.
Delays and Downtime
Time is money. When repairs drag on because someone underestimated the job or ran into “unexpected” issues, it affects your bottom line.
Safety Hazards
Untrained crews might skip safety steps or use faulty equipment, putting themselves—and your staff—at risk.
Long-Term Cost Implications
A cheap fix today could mean a total replacement in a year. Bad workmanship snowballs into bigger problems down the line.
Benefits of Hiring Experienced Contractors
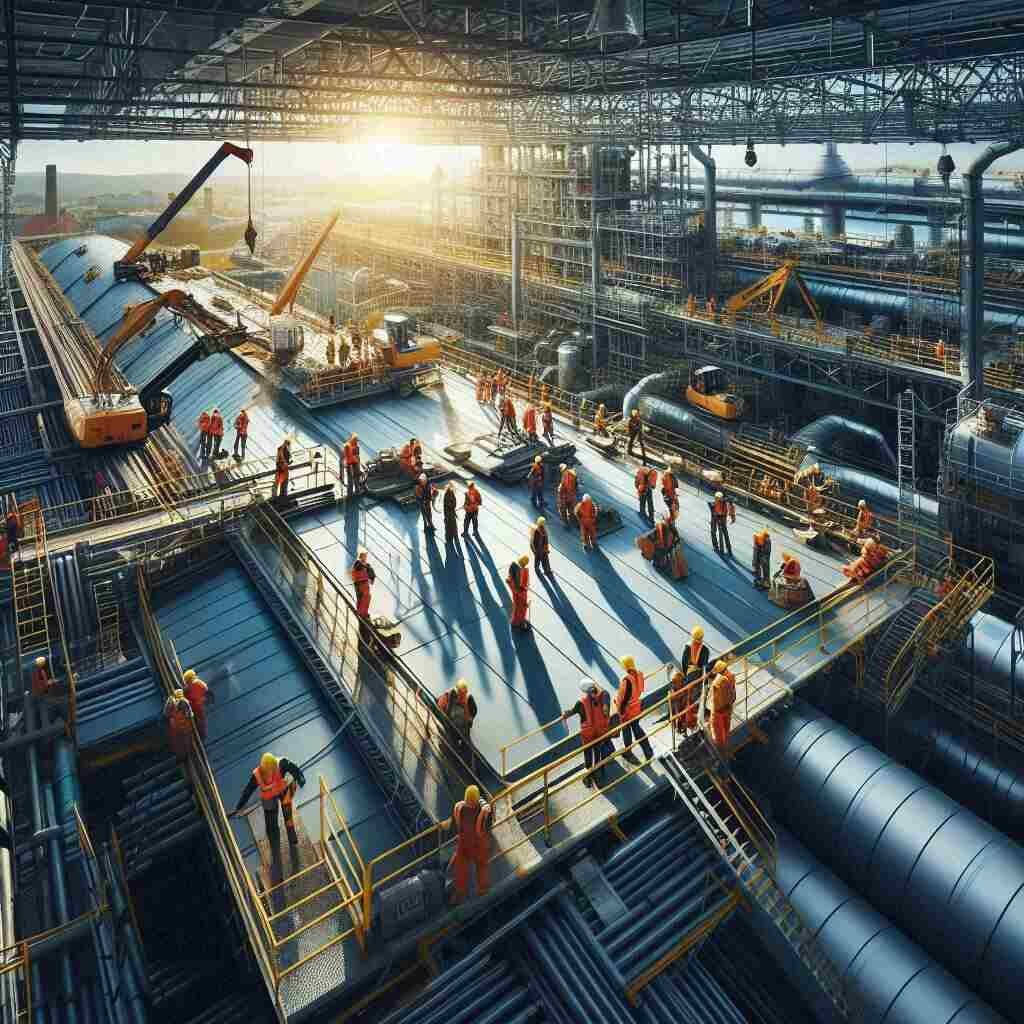
Proven Track Record
They’ve been there, done that. You get someone who’s seen all kinds of roof damage and knows exactly how to fix it efficiently.
Deep Technical Knowledge
From infrared leak detection to structural decking repair, experienced contractors bring advanced skills to the table.
Efficiency and Timeliness
They can quote realistic timelines—and stick to them. That means less disruption and a faster return to normal.
Adherence to Safety Standards
You won’t have to babysit. Experienced pros come with their own safety protocols, training, and certifications.
Warranty and Post-Repair Support
Good contractors stand by their work. Many offer extended warranties and follow-up service, so you’re not left hanging.
How Experience Translates Into Better Project Management
Accurate Project Estimates
A seasoned contractor won’t just throw out a number—they’ll do site visits, analyze the damage, and give you a precise estimate.
Effective Communication
Experienced teams keep you in the loop at every stage, from initial assessment to completion. No ghosting or surprises.
Flexibility in Facing Challenges
Weather delay? Hidden structural issue? A pro can pivot without blowing your schedule or budget.
Industry Certifications and Credentials to Look For
OSHA Certification
It’s a must. Certified contractors show they take worker and site safety seriously.
Manufacturer Training and Licensing
If your roof is made of a specific brand’s material, check if the contractor is licensed to install or repair it.
Insurance and Bonding
Never hire someone without proof of liability insurance and bonding. That’s your protection in case something goes wrong.
Real-World Examples of Experience Making a Difference
Case Study: Emergency Roof Repair During Harsh Weather
An industrial warehouse in the Midwest suffered storm damage. An experienced contractor mobilized a crew overnight, stabilized the roof, and prevented inventory loss.
Case Study: Large-Scale Commercial Warehouse Retrofit
A food processing facility needed a total roof retrofit without shutting down operations. Only a veteran team could juggle timelines, hygiene requirements, and logistics successfully.
Key Questions to Ask Before Hiring a Roofing Contractor
What’s Your Experience With Industrial Roofing?
Make them show, not just tell. Ask about similar projects they’ve completed.
Can You Share References or Case Studies?
Happy clients are a good sign. Reach out and ask about their experience firsthand.
What’s Your Safety Protocol Like?
A vague answer here is a red flag. Reputable contractors will explain their safety plan in detail.
How to Find the Right Industrial Roofing Contractor
Online Reviews and Ratings
Google, Yelp, and BBB reviews can give you a snapshot of how a contractor performs.
Checking Past Projects
Ask to see a portfolio or project list. Look for jobs similar in size and complexity to yours.
Conducting Interviews
Meet in person (or over video), and treat it like a hiring process. You’re trusting them with a big job—do your due diligence.
The Cost Factor: Cheap vs. Value-Based Decisions
The Illusion of Savings
Cutting corners might save you upfront—but it’ll cost you more in repairs, downtime, and frustration later.
Investing in Long-Term Reliability
A slightly higher price tag for a reputable contractor is an investment in peace of mind and long-term savings.
Common Types of Industrial Roof Repairs
Leak Detection and Sealing
Leaks don’t just drip—they damage insulation, walls, and equipment. Finding and fixing them fast is crucial.
Full Roof Replacement
Sometimes, patching won’t cut it. Replacing the roof is a big job, and only the most experienced should take it on.
Preventive Maintenance Services
The best repair is the one you never need. Regular maintenance prevents costly issues before they happen.
The Role of Maintenance Contracts
Scheduled Inspections
Routine checks catch problems early—before they escalate.
Quick Response to Damage
When you have a contract, you’re a priority client. That means faster service when something goes wrong.
Budget Management Over Time
A maintenance plan spreads costs out, helping you avoid budget shocks from emergency repairs.
Environmental and Energy Considerations
Energy-Efficient Roofing Materials
Experienced contractors can recommend reflective coatings or insulation upgrades that cut your energy bills.
Sustainable Repair Techniques
Some pros offer eco-friendly options like green roofs, solar integration, or recycled materials.
Future-Proofing Your Roof With the Right Contractor
Technology and Innovation in Industrial Roofing
Drone inspections, infrared scans, and predictive maintenance are just a few modern tools in an experienced contractor’s toolbox.
Planning for Expansion or Retrofitting
Got big plans? Your contractor should help design a roof that’s ready for future growth or tech upgrades.
Conclusion
Recap of the Value Experienced Contractors Bring
Industrial roofing is no place to cut corners. Experienced contractors bring more than skills—they bring foresight, planning, and peace of mind.
Final Thoughts on Making the Right Choice
Choose wisely. The right contractor won’t just fix your roof—they’ll protect your entire operation from disaster and downtime.
❓ FAQs
1. How do I verify a contractor’s industrial roofing experience?
Ask for case studies, licenses, certifications, and references from past industrial clients. Don’t hesitate to reach out and ask tough questions.
2. What should be included in a roofing contract?
Scope of work, materials, timeline, cost estimate, warranty, and safety protocols should all be clearly listed.
3. How often should an industrial roof be inspected?
At least twice a year—once in spring and once in fall—and after any major weather event.
4. Are experienced contractors more expensive?
Sometimes upfront, yes. But their work saves you money in the long run by avoiding future issues and extending your roof’s lifespan.
5. What signs indicate I need industrial roof repair?
Visible leaks, pooling water, damaged flashing, insulation issues, and unusually high energy bills are common red flags.